FESTO launches energy-saving control pneumatics with piezo technology
2024-03-17The production of tires and wafers seems entirely unrelated. However, from an automation technology perspective, they both utilize the same control pneumatic technology. Festo has further advanced compressed air technology to be more sustainable, resource-saving, and energy-efficient.
In “Controlled Pneumatics,” Festo combines proportional technology, sensors, and control algorithms to form control loops. These are mechatronic pneumatic systems equipped with valve and communication technology that enable digital influence, based on sensor variables.
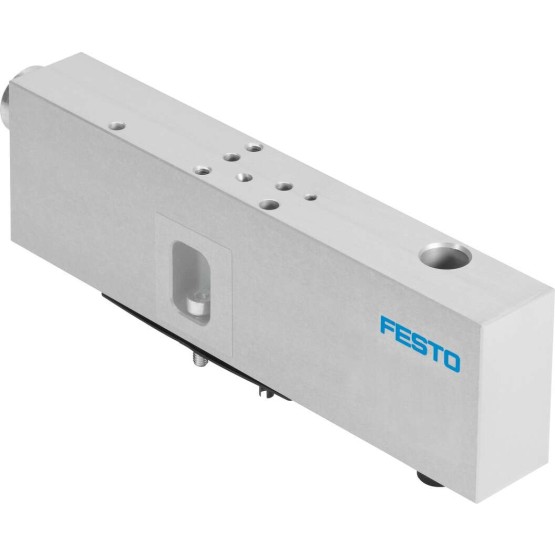
This technology particularly creates new application fields for pressure and flow control, surpassing the limits of pneumatics and offering simpler, more stable, faster, more accurate, and more efficient solutions. On the other hand, conventional standard pneumatic devices are primarily used in simple applications like point-to-point movements. The simplicity of standard pneumatic devices is evaluated as an ideal solution, especially in many cases.
Digitalized Pneumatics
A typical example of Festo’s digitalized pneumatics is the Festo Motion Terminal VTEM, used to digitalize pneumatics. This automation platform can replace over 50 individual components within a compressed air control circuit, utilizing piezo technology and Motion Apps.
Applied to tire production, this technology could bring savings in the loading process. Festo Motion Terminal utilizes the Motion App feature “Selectable Pressure Levels” to smoothly supply green tire blanks (unprocessed tires without ground contact) to presses. If variations in handling systems are minimal during loading, the supply speed can be increased. Each tire’s processing time can be accelerated by several seconds. Although initially seemingly insignificant, with approximately 1.8 billion car tires produced annually, this could amount to a considerable sum for each tire manufacturer. Another advantage of controlled pneumatic devices is that they significantly increase the service life of parts by reducing impact forces.
Less Pressure = Less Energy Consumption
In fact, by accelerating loading operations and reducing pressure, compressed air consumption is reduced, hence requiring less energy. Calculations show that, compared to standard pneumatic devices, almost 33% of compressed air savings can be achieved with horizontal installations of DSBC cylinders, and nearly 75% with vertical installations of the same cylinders. Just by controlling vertical and horizontal cylinders, about 60% energy savings can be achieved in these loading and unloading operations.
Predictive Maintenance
Motion App “Leakage Diagnosis” is also used for simplifying maintenance and automatically monitoring leaks. Thus, faults can be detected and diagnosed accurately with defined diagnostic cycles and thresholds. As a result, a reliable basis for predictive maintenance is established.
Festo Motion Terminal can prevent faulty air ducts, hence preventing an increase in compressed air supply in case of leaks. Thus, this innovative automation platform prevents unnecessary air consumption.
Preventing Wear with Piezo Technology
If transporting and storing wafers in the semiconductor industry, Festo’s N2 purge system prevents wafer oxidation by supplying inert nitrogen continuously to the atmosphere around the wafer. This flow control, also known as Mass Flow Controller (MFC), is based on piezo technology and integrated sensor technology.
The design of piezo valves reduces the risk of gas flow contamination due to particle wear, with peaks of about 0.1 micrometers particle size generated per switching cycle. Traditional solutions produce five times the particle content. The piezo technology used prevents wear due to friction, thus extending the valve’s service life. Operating and maintenance costs are significantly reduced compared to traditional solutions.
Cost Savings through Low Inherent Energy Consumption
Due to design, directly operated flow controllers reduce the risk of leaks. Electricity consumption is less than 1 watt. This is 80% less than traditional solutions in both cases. Closed-loop control minimizes hysteresis while ensuring precise, stable, and linear movement of the flow. Testing accuracy is +/-0.25% of the set value.
Through “Controlled Pneumatics” and related digitalization and piezo technology, Festo has elevated compressed air technology to a new level of resource conservation, energy efficiency, and sustainability.
Additionally, Festo is a global company headquartered in Esslingen am Neckar, Germany, an independently owned family company. Since its founding, Festo has set standards in industrial automation technology and technical education, contributing to sustainable development in the environment, economy, and society. Supplying factory and process automation customers to over 350,000 customers in more than 35 industries, Festo has achieved sales of approximately €3.36 billion in 2021, with around 27,000 employees at more than 250 locations in 61 countries.