Enhanced Technology Hoses vs. EPDM Hoses: A Comparative Overview
2024-08-02In industrial and manufacturing sectors, the choice of hose is crucial. Hoses play a vital role in transferring liquids, gases, and particulates, and must withstand high pressure, high temperature, and chemical corrosion. This article introduces two widely used types of hoses: enhanced technology hoses and EPDM (Ethylene Propylene Diene Monomer) hoses, highlighting their differences in structure, materials, performance, and applications.
Enhanced Technology Hoses
Structure and Materials
- Reinforcement Materials: Enhanced technology hoses typically consist of multiple layers, including an inner tube, a reinforcement layer, and an outer cover. The reinforcement layer may include braided steel wire, synthetic fibers, or metal mesh to enhance the hose’s strength and pressure resistance.
- Variety of Materials: The inner tube and outer cover materials can be chosen based on specific applications, such as rubber, PVC, PU, etc.
Performance
- Pressure Resistance: Due to the presence of the reinforcement layer, enhanced technology hoses have a high-pressure resistance, making them suitable for high-pressure environments.
- Abrasion Resistance: The reinforcement layer also improves the hose’s abrasion resistance, making it more durable under mechanical stress.
- Flexibility: Depending on the reinforcement materials and structure, the flexibility of enhanced technology hoses can vary, but they are generally stiffer than regular hoses.
Applications
- Industrial Use: Widely used in high-pressure hydraulic systems, pneumatic systems, and chemical transportation, where high strength and high pressure resistance are required.
- Special Applications: Suitable for environments requiring resistance to twisting and vibration, such as in machinery and construction sites.
EPDM Hoses
Structure and Materials
- Single Material: EPDM hoses are primarily made of ethylene propylene diene monomer, a synthetic rubber known for its excellent weather resistance, heat resistance, and chemical resistance.
Performance
- Weather Resistance: EPDM hoses perform exceptionally well when exposed to sunlight, ozone, and climate changes, making them suitable for outdoor use.
- Heat Resistance: Capable of maintaining performance stability in high-temperature environments, typically with a temperature range of -40°C to +150°C.
- Chemical Resistance: Resistant to many chemicals, such as acids, alkalis, and salts.
- Flexibility: Generally more flexible than enhanced technology hoses, making them easier to handle and install.
Applications
- Automotive Industry: Widely used in automotive cooling systems, heating systems, and air conditioning systems.
- Building and Roofing: Used in roofing membranes, drainage systems, and other applications requiring long-term weather resistance.
- General Industry: Suitable for low-pressure applications needing heat and chemical resistance, such as food-grade transport lines and steam hoses.
Summary
Enhanced technology hoses and EPDM hoses each have their own advantages and are suitable for different application environments. Enhanced technology hoses, with their high pressure and abrasion resistance, are ideal for high-strength and high-pressure conditions. In contrast, EPDM hoses are renowned for their excellent weather, heat, and chemical resistance, making them perfect for outdoor and high-temperature environments. Selecting the appropriate hose type based on specific application needs ensures system reliability and longevity.
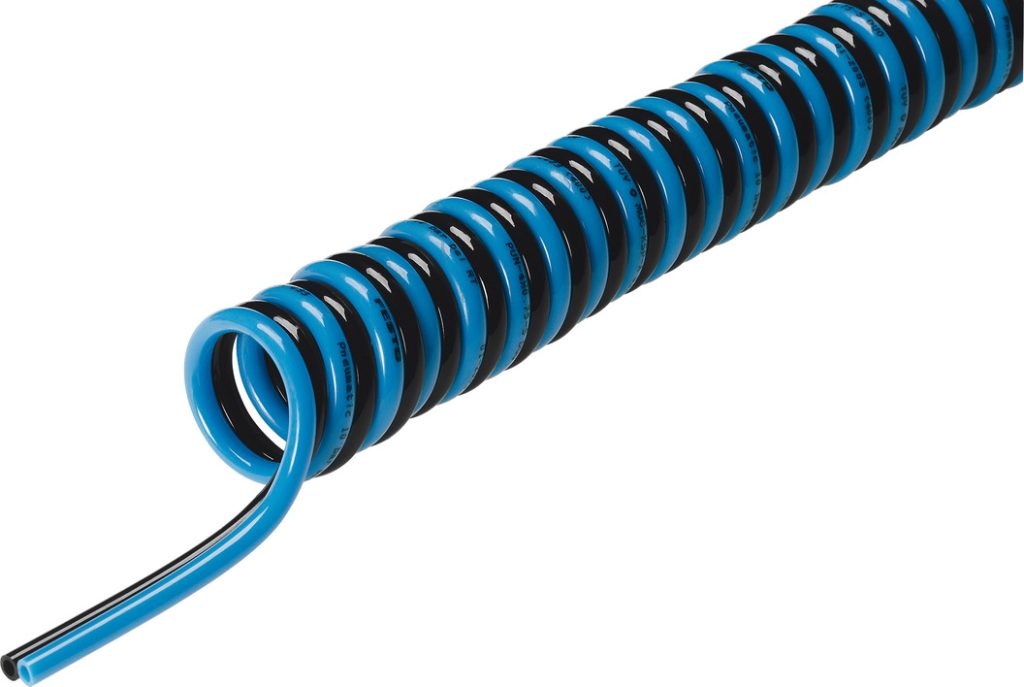