Maintenance Mishaps: The Chaos of an Unexpected Flow Test and Separator Failure
2024-09-18In the industrial setting, compressed air systems are an essential component, providing power to a variety of machinery and tools. However, these systems require regular maintenance and inspection to ensure their efficient and safe operation. This article will detail an unexpected incident encountered by a compressed air auditor during a routine flow test of an old compressor, as well as the subsequent issues that arose.
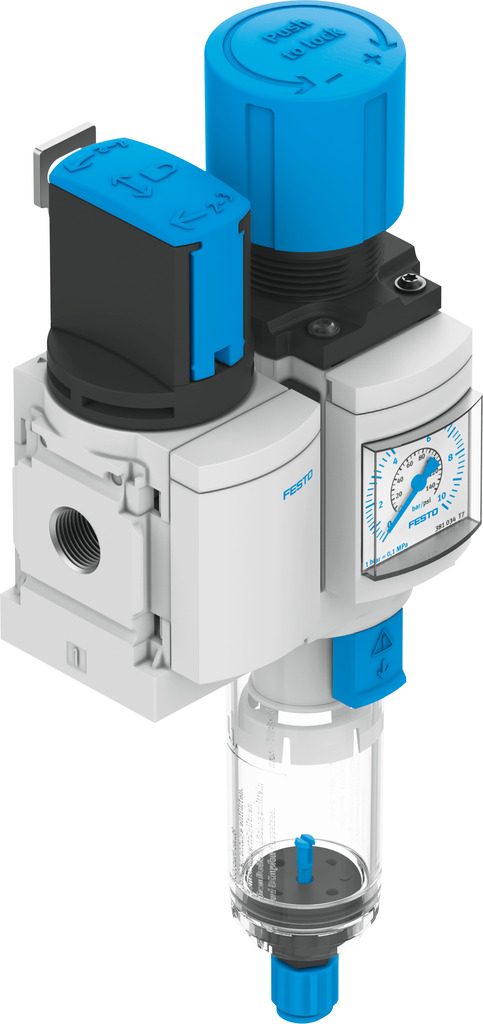
The Importance of Flow Testing
Flow testing is a critical step in assessing the performance of a compressor. It helps determine whether the compressor can provide sufficient compressed air to meet the demands of a factory. The test typically involves using a device with various calibrated orifices, such as the LP-07, which can simulate different flow requirements. By opening orifices of different sizes and measuring the pressure, the auditor can calculate the actual output of the compressor.
The Unexpected During Testing
During a routine flow test, the auditor encountered an unexpected situation. The air/oil separator of the compressor suddenly failed, causing all the ATF (Automatic Transmission Fluid) lubricant to be released in a torrential flow. Since each orifice was connected to a silencer, these silencers, under pressure, suddenly acted as showerheads, spraying lubricant in all directions, including onto the auditor himself.
Consequences of Separator Failure
Such a separator failure not only caused embarrassment and inconvenience to the auditor but could also lead to more serious consequences. The leakage of lubricant would contaminate downstream compressed air filters and dryers, and could even clog the pipelines. This would not only affect the efficiency of the system but also result in costly cleanup and repair expenses.
Preventive Measures
To avoid such catastrophic failures, auditors and maintenance teams need to closely monitor the condition of the separator. This includes regular checks of the separator’s pressure differential and the amount of lubricant residue. Additionally, strictly adhering to the manufacturer’s maintenance specifications, especially regarding operating hours, is crucial.
Conclusion
Although this incident was unpleasant for the auditor, it also served as a reminder of the importance of regular equipment checks for the maintenance team. Through timely maintenance and inspection, similar failures can be avoided, ensuring the stable operation of compressed air systems. For the auditor, this experience, though unpleasant, provided valuable lessons that in the industrial environment, prevention is always better than cure.