SMC Digital Compressed Air Management: The Future of Production Efficiency and Energy Management
2024-11-16SMCIntroduction: Energy Management and Compressed Air Efficiency
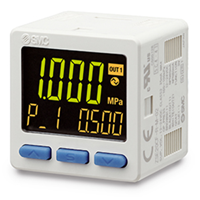
In today’s manufacturing landscape, energy management has become a top priority for industrial facilities worldwide. With the growing need for energy efficiency and sustainability, businesses are actively seeking solutions to reduce energy waste and optimize consumption. One critical area where energy efficiency can be significantly improved is compressed air systems, which are among the highest consumers of energy in many industrial processes. Enhancing compressed air management has thus become a key strategy for reducing overall energy consumption and improving operational efficiency.
The advent of digital technology has revolutionized how compressed air systems are managed. Modern wireless and digital solutions now enable real-time monitoring and data collection, empowering businesses to make more informed decisions. By adopting digital compressed air management, companies can not only improve energy efficiency but also gain better control over their production processes, reducing waste and optimizing the use of resources.
The Core of Digital Compressed Air Management: Real-Time Data Collection and Analysis
One of the core advantages of digital compressed air management systems is their ability to collect and transmit real-time data on key parameters such as flow rate, pressure, temperature, and speed. Modern systems like SMC’s AMS series are capable of monitoring compressed air usage through various communication protocols such as EtherNet/IP, Profinet, and EtherCAT. These systems allow for seamless integration and real-time data collection across the entire compressed air network, making it possible to monitor system performance continuously.
For example, data is collected at frequencies up to 10Hz, ensuring that a large amount of information is captured every second. These data points are then transmitted at a reduced frequency of 1Hz through protocols like OPC UA, allowing them to be sent directly to the cloud or a data warehouse for further analysis. This real-time data not only provides insights into current system performance but also enables predictive analytics, helping companies anticipate issues before they arise and make data-driven decisions to optimize operations.
Through such systems, manufacturers can quickly identify inefficiencies like air leaks, pressure drops, or malfunctioning equipment. By addressing these issues promptly, companies can avoid unnecessary energy consumption and reduce overall costs.
Flexibility and Scalability: From Localized Optimization to Holistic Management
As production demands evolve, companies need systems that can scale and adapt to changing requirements. Modern digital compressed air management solutions offer impressive flexibility, allowing for easy expansion of the system as needed. For instance, SMC’s AMS systems support up to 10 remote units connected wirelessly to each central unit. This scalable architecture means that even as the number of devices and data points grows, the system can handle the increased load without affecting network bandwidth or overall system performance.
The next level of scalability comes with the integration of additional data sources into the system. Digital systems are no longer limited to monitoring compressed air alone; they can now integrate data from a wide range of other sources, including energy consumption, water usage, vibration monitoring, and other critical performance indicators. This holistic approach enables businesses to manage all their key resources and processes from a single platform, making it easier to track and optimize the entire production environment.
This integrated approach to resource management not only helps businesses save costs but also leads to a more efficient use of energy and materials. By centralizing data collection and analysis, manufacturers can achieve more comprehensive insights into their operations and make smarter decisions across the entire production process.
Wireless and IO-Link Technologies: Simplifying Installation and Expansion
One of the key challenges in traditional compressed air systems is the complexity of installation and wiring, especially when adding new devices or expanding the system. Modern digital solutions address this issue by integrating wireless and IO-Link technologies, making it easier to scale and connect devices without the need for extensive wiring.
For example, SMC’s EXW1 compact wireless system allows businesses to connect multiple devices—including third-party equipment—without the need for physical cables. This wireless communication significantly reduces installation time and costs, as well as the physical limitations posed by traditional wired networks. The use of IO-Link further enhances this flexibility, allowing data from a wide range of devices to be transmitted along a single communication bus, reducing the need for separate communication channels for different manufacturers.
Additionally, systems equipped with redundant IO-Link ports can easily accommodate up to 10 additional devices, further expanding the network’s capacity. This seamless integration of new devices into the system creates a robust and scalable network that supports a wide range of industrial equipment, all while maintaining high data transmission speeds and reliability.
The Future of Digital Compressed Air Management
Digital compressed air management is not just about improving the efficiency of compressed air usage—it represents a broader shift toward more intelligent, integrated production management. By enabling real-time data collection, analysis, and decision-making, digital systems provide businesses with the tools they need to optimize resource usage, reduce costs, and improve operational efficiency across the entire production process.
Looking ahead, the digital management of compressed air will play a critical role in the transition to smart factories and the broader concept of Industry 4.0. With continuous innovation and the development of more advanced technologies, future compressed air management systems will become even more intelligent, connected, and capable of meeting the increasingly complex needs of modern manufacturing. By adopting these solutions, companies can stay ahead of the curve, improving their operational efficiency, reducing energy consumption, and enhancing their competitiveness in a rapidly evolving market.
In conclusion, SMC digital compressed air management is not just an operational improvement; it is a strategic step toward building more efficient, sustainable, and intelligent production systems for the future.