Pneumatic Actuators, Valves, and Manifolds – An Overview of Solutions and Trends
2024-05-29Table of Contents
- How to Choose the Right Pneumatic Actuator for a Specific Application?
- Manifolds: Advantages and Service Life in Applications
- Direction and Development Trends of Pneumatic Components
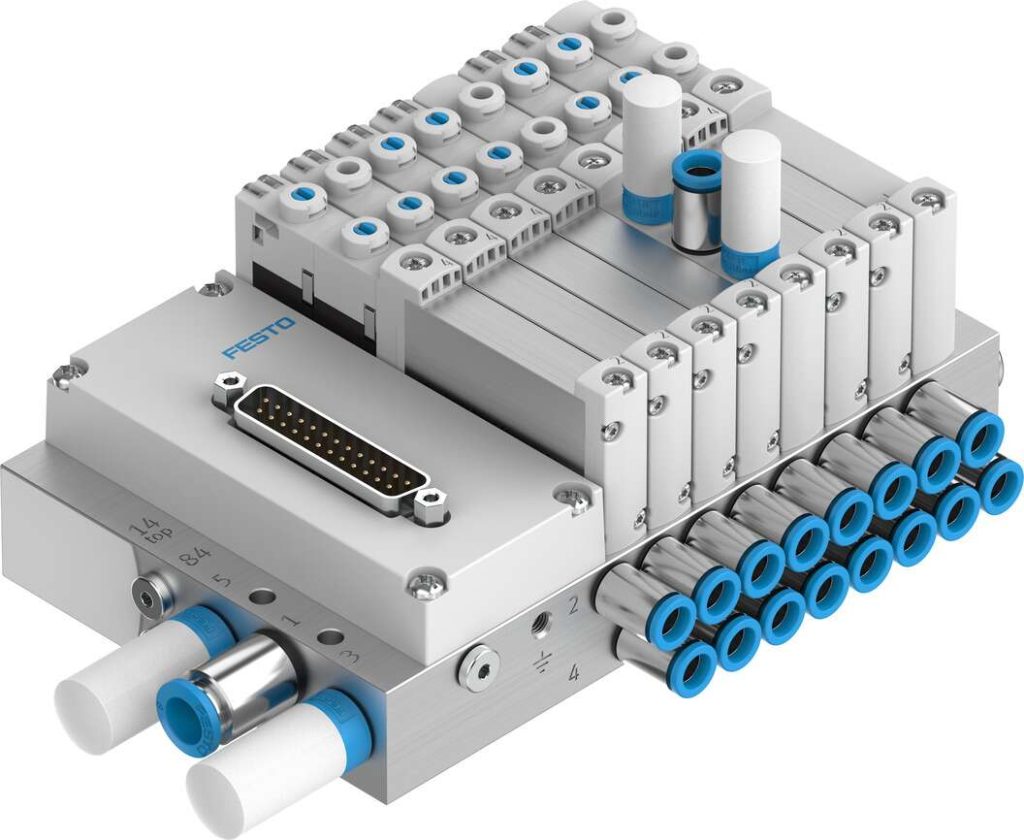
Introduction
Pneumatic actuators, valves, and manifolds are crucial structural components in the construction of automated systems. This article will delve into the selection, advantages, service life, and latest technological trends of these key components to help you maximize the potential of these components.
How to Choose the Right Pneumatic Actuator for a Specific Application?
Selecting the right pneumatic actuator is a technical process that requires consideration of the following key steps:
- Piston Diameter Selection: Ensure that the cylinder can provide the appropriate operating force under the assumed compressed air pressure.
- Stroke Determination: Choose the appropriate stroke length based on the type of cylinder (piston rod cylinder or rodless cylinder).
- Compatibility with Automatic Control Systems: Consider whether a cylinder with a magnet and the corresponding piston position sensor is needed.
- Operating Conditions Assessment: Including cycle frequency, load method, and environmental conditions.
- Actuator Type Selection: Choose the actuator type based on installation space and method (fixed or swinging).
- Installation Components Selection: Consider the components connected to the cylinder and those mounted on the piston rod.
In the actual purchase process, in addition to technical factors, the price-to-quality ratio of the actuator from specific suppliers should also be considered.
Manifolds: Advantages and Service Life in Applications
Manifolds have been used in pneumatic systems for many years, and their advantages include:
- Versatility: Suitable for a variety of application scenarios.
- Control Capability: Capable of controlling cylinders of any diameter.
- Space Saving: Can be installed even in places with limited space.
- Reduction of Auxiliary Components: Reduces the number of connectors, silencers, etc.
- Wiring Simplification: Reduces wiring volume, simplifying the installation process.
- System Integration: Can be integrated with other devices used in industrial automation systems, including the latest Industry 4.0 solutions.
- Comprehensive Diagnosis: Provides system diagnostics and generates warnings of improper operation.
- Energy Optimization: Reduces the amount of compressed air and power required for control.
The service life of manifolds depends on various factors, including the correct preparation and maintenance of compressed air. Proper filtration, moisture removal, and appropriate supply pressure are key to ensuring the long-term stable operation of manifolds.
Direction and Development Trends of Pneumatic Components
In recent years, the development in the field of pneumatic components has focused on the following areas:
- Material Optimization: Increasing the application of plastics in pneumatic actuators to reduce weight and improve energy efficiency.
- Energy Efficiency Improvement: Developing a series of pneumatic components that operate at a lower standard pressure, such as SMC’s 4 bar standard pressure series.
- Component Lightweighting: Continuously reducing the weight of cylinder components to improve response speed and energy efficiency.
- Self-Adjusting Pneumatic Suspension: Increasingly popular, offering better performance and comfort.
- Energy-Saving Products: Launching a series of energy-saving products, such as energy-saving actuators and energy-saving pressure reduction valves.
Conclusion
With the continuous advancement of technology, the role of pneumatic actuators, valves, and manifolds in automated systems is becoming increasingly important. Choosing the right components and understanding their advantages and development trends are crucial for building efficient and reliable automated systems. I hope this article provides you with valuable insights and guidance.